Electrical Engineering
(ROADWAY LIGHTING)
Saint Andrews Lock and Dam (SALD) Bridge Roadway and East Warehouse Lighting and Electrical Upgrades
Intent:
The goal is to provide current electrical record drawings and to rehabilitate and upgrade the Bridge Roadway, Canal, Lock Entrance Sign and Flag Pole, the Bridge Under Deck, and the East Side Warehouse lighting and achieve design excellence as recognized by the Engineering industry through the application and integration of design and construction industry standard best practices and procedures.
Objectives:
Design and Construction result are to be effective and efficient, meet current Codes, Standards and guidelines, optimize performance of the system, factor in ease of maintenance, aesthetically pleasing, minimize long-term maintenance over 25-year life span.
Scope:
Undertake a detailed evaluation of the entire Electrical System(s) to produce current electrical record drawings and rehabilitate and upgrade the lighting system and controls.
Technical challenges and problems that were encountered during design:
- Inaccuracy of existing drawings required detailed site investigations to verify existing conditions.
- Integral systems and equipment operating intermittently, significantly aged/pushed past useful life and/or overloaded.
- Heritage considerations requiring balancing preserving character with compliance.
- Tight budget control required strict adherence to diligent costing and control.
- Managing at times conflicting objectives of many stakeholders all equally invested in the project.
Design & Construction Approaches used to meet project requirements & steps taken to address challenges/resolve problems:
HDK’s approach is “client”-centric from the start; ask questions during the initial interface, work collaboratively all parties, integrate the Project Brief directly into our team’s Work Breakdown Structure, diligently monitor and manage schedule, cost and quality throughout project stages, align submissions to key milestone dates and submit in advance to allow adequate review time and more. This approach was informed by ongoing technical input; HDK’s analysis consisted of evaluating power system infrastructure within context of site-specific loads, projected design loads, system architecture, electrical safety and security, Code compliance, and operation requirements.
All these came into play throughout the design and construction stages and were used to address coordination issues within and external to the consulting team (i.e., Authorities Having Jurisdiction, obtaining buy-in from various stakeholders, etc.) as well as designing with construction in mind; requirements were such that the facility had to stay open during both design and construction requiring project phasing during the latter stage.
Cross-cutting challenges included limited funding available, balancing unique heritage nature, Code compliance and performance requirements (i.e., systems to achieve at least 30% more energy efficiency than the Model National Energy Code for buildings).
SCHEDULE
Design Start:
Construction Complete:
June 2016
Feb 2017
PROJECT BUDGET
Construction Budget:
$3.5M
Key Disciplines:
- Electrical Engineering
- Mechanical Engineering
- Structural Engineering
- Civil Engineering,
- Architectural,
- Cost Consulting,
Design & Construction Budgets, Final Costs and Explanation of Variances:
DESIGN
Initial budget kept private by client.
Classes of Cost Estimates (000’S)
C | B | A |
$504.4 | $545.4 | $566.5 |
The design stage saw minimal changes in the design cost from approved 50% design to final submission which were approved for tender with minor changes.
CONSTRUCTION
Award Value:
$315,000.00
Final Cost:
$323,732.31
The contract value increased by less than 5% or $8,732.31 over the course of construction. Two Contract Change Notices were issued for approved added requirements: Heated, insulated enclosure for Centre Bridge and Desk Shed Lighting Controls (001, $6,654.59) and Fish Ladder Additional Light (002, $2,077.72).
Explanation of Changes in Project Scope:
Owner initiated changes were the only changes during project implementation; heated, insulated enclosures for the Centre Bridge and Desk Shed lighting controls and additional lighting added to the Fish Ladder.

More Projects
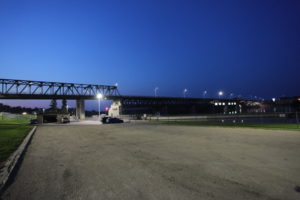
St. Andrews Lock & Dam (SALD) Lighting and Electrical Upgrades
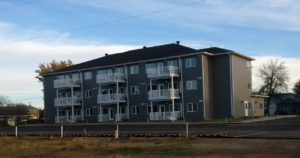
New build, low-rise, multi-unit apartment complexes
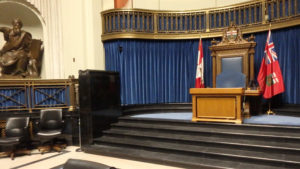
Security Systems Upgrades at Manitoba Legislative Assembly Building
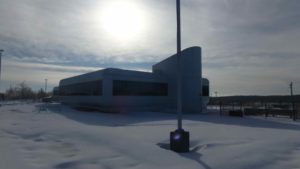
CFB Halifax MARLANT Condition Assessment and Recommissioning Study
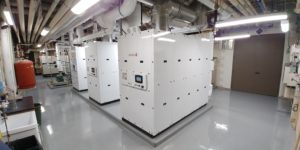
GHG Reduction Mechanical Upgrades at a National Research Centre
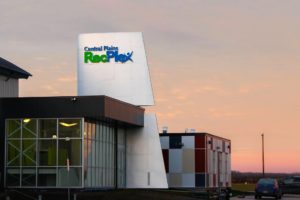